In-Plant Conveyors
In-plant conveyors form the backbone of many operations and are utilized within the mining, minerals processing, paper & pulp and power generation industries to receive/unload, stockpile, reclaim and deliver various material types within a plant.
Interconnecting system equipment
In-plant conveyors interconnect system equipment within brownfield or greenfield operations. Such equipment can range from ship, barge, wagon (railcar) or truck loaders and/or unloaders, as well as stackers, reclaimers, storage bins/hoppers, feeders, crushers, screens and other equipment.
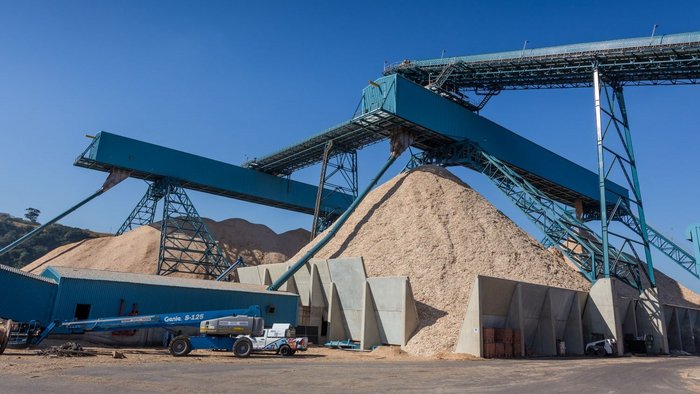
Flexibility and reliability
The focus for such conveyor solutions is to easily integrate within the existing constraints of your operations and/or be sufficiently flexible to expand and adapt to changing requirements as new equipment, lines or capacity increases are added to your operations.
As simple as it sounds, such conveying systems need to be designed with robustness and reliability from the start with the capability to efficiently operate under arduous conditions day-in-and-day out, reducing downtime and increasing overall operational efficiency.
Continued focus on flexibility with varied specifications according to specific handling requirements
Conveyor lengths can vary from short distances of just a few meters up to ~1.6 km (1 mi) or so. Belt widths are typically between ~450 mm (18 in) and ~2,135 mm (84 in) depending on the capacity, application and client/project requirements. As such, conveying capacities can vary from just a few tons per hour up to ~7,500 t/h.
Such conveying solutions can be located indoors or outdoors and can be constructed of simple stringers and post supports, or be elevated on deck-type trusses, or in rectangular or tubular galleries.
Depending on requirements, in-plant conveyors can also integrate belt scales, metal detectors, magnetic separators and various types of material analyzers and sampling equipment.
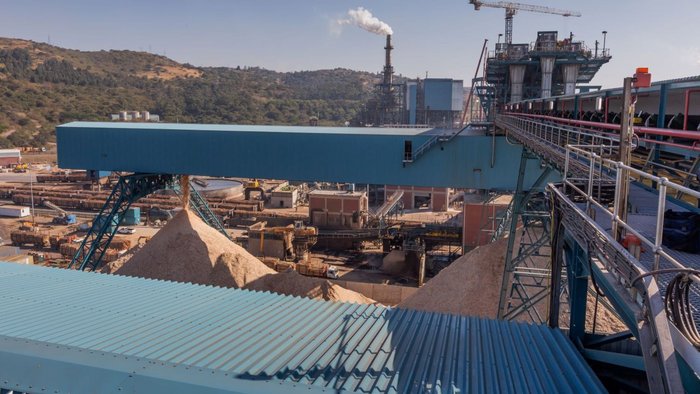
Downloads
References
-
In-plant conveyor system for a silver-copper mine in Chile
Customer Project Name Mina Ministro Hales CODELCO Calama, Chile 2013 In-plant conveyor system for a silver-copper mine in Chile
Delivery of the complete in-plant conveyor system to handle copper ore, copper pebbles and steel balls including:
- 15 in-plant belt conveyors from 450 mm (18 in) to 1,525 mm (60 in) in width and a total installed length of 2,100 m - also including 2 high-angle (pocket) belts
- 3 transfer towers with complete transfer chute arrangemen
- Ancillary equipment supplied included belt scales and conveyor fieldbus system
Project figures
15 conveyors approx. 2,100 m overall length 3 10 t/h to 3,500 t/h -
In-plant conveyor system for a mine mouth coal fired power plant in USA
Customer Project Name Prairie State Energy Campus Prairie State Generating Company Illinois, USA 2008 In-plant conveyor system for a mine mouth coal fired power plant
Delivery of the complete in-plant conveyor system for a coal fired power plant including wagon (railcar) unloading hopper, stacking tubes (lowering wells), storage dome, crusher tower, transfer towers and traveling trippers.
- 12 in-plant belt conveyors from 762 mm (30 in) to 1,525 mm (60 in) in width and a total installed length of 3,000 m for the handling of coal and limestone
- Transfer towers with complete transfer chute arrangement
- Ancillary equipment supplied included belt scales, magnetic separators and metal detectors
Project figures
12 conveyors and 4 belt feeders approx. 3,000 m overall length 750 t/h to 3,600 t/h -
In-plant conveyor system for a mine mouth coal fired power plant in Australia
Customer Project Name Millmerran Power Project Millmerran Power Partners Queensland, Australia 2001 In-plant conveyor system for a mine mouth coal fired power plant
Delivery of the complete in-plant conveyor system for a coal fired power plant including 500 ton truck dump hopper, feeder breaker, linear stacker, portal reclaimer, secondary & tertiary crushing crusher tower, transfer towers and traveling trippers.
- 11 in-plant belt conveyors from 1,067 mm (42 in) to 1,372 mm (54 in) in width and a total installed length of 3,500 m for the handling of coal
- Transfer towers with complete transfer chute arrangement
- Ancillary equipment supplied included belt scales, magnetic separators and metal detectors
Project figures
11 conveyors approx. 3,500 m overall length 990 t/h to 1,980 t/h
CONTACT US
Do you have any questions or would you like further information?
We look forward to your inquiry at: info@takraf.com