Horizontal vacuum belt filters for dewatering
DELKOR belt filters boast low capital, running and maintenance costs and thereby outperform traditional filter technologies in all situations where capacity, efficient cake washing and minimum liquor dilution are required.
DELKOR’s technology and know-how is founded in the horizontal vacuum belt filter and we remain the supplier of the world’s largest individual machine. DELKOR filters are suitable for dewatering a wide range of commodities with a number of installations across various commodities around the world.
DELKOR Horizontal Vacuum Belt Filters
Utilizing vacuum filtration, the horizontal belt filter is an efficient and reliable liquid/solid separation machine suitable for dewatering various commodities such as iron ore, mineral sands, lead zinc concentrates, fine coal flotation concentrates, phosphoric acid filtration and others. They can be employed as stand-alone machines or in combination with other filtration processes.
Features and technical specification:
- Sizes from effective area of 1 m2 to 162 m2 as a single machine and design up to 300 m2
- Design and selection of Material of Construction (MoC) and its ancillaries to suit process
- Supplied >850 filters around the world in which >35 % boast a belt width above 3.2 m
- Controlled cycle time to cater to filtration and cake wash times by controlling drive through Variable Frequency Drive (VFD)
Acid Filtration and now Tailings Filtration too
Over the years, DELKOR pioneered the use of belt filters for acid filtration and various other applications driven through unparalleled expertise and experience – case in point, our belt filters are now also well accepted for tailings filtration.
Dewatered tailings can either be used as mine backfill or sent straight to the Dry Stack Tailings (DST) impoundment. This results in a technically viable and economically feasible solution to handle process plant tailings in the safest and most environmentally friendly manner.
MAX-FeED belt feeder - reducing costs whilst increasing the performance of vacuum belt filters
Application of DELKOR’s MAX-FeED belt feeder on existing belt filters at a major iron ore site in Australia has highlighted strong improvements in belt filter performance (throughput (66 % increase) and consistency of filter cake characteristics). This, together with DELKOR test work, has indicated the potential to significantly reduce the number or the size of the filter, which results in reduced capital, transportation, installation and operational costs, together with a reduction in spares and overall maintenance and equipment footprint - and with no additional ancillary equipment required.
This significantly improved performance is a result of advanced features incorporated into the DELKOR MAX-FeED that overcome some of the challenges with existing feeders.
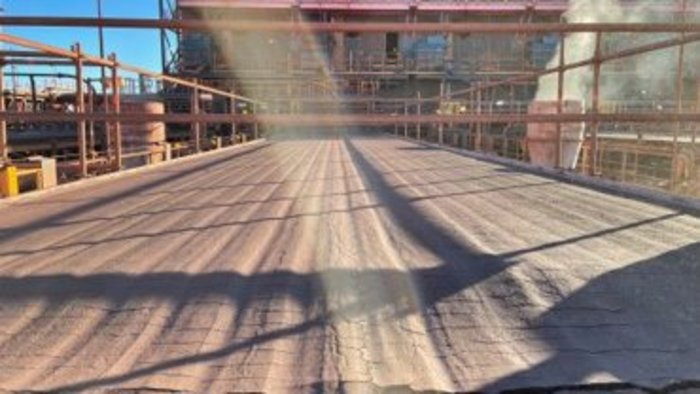
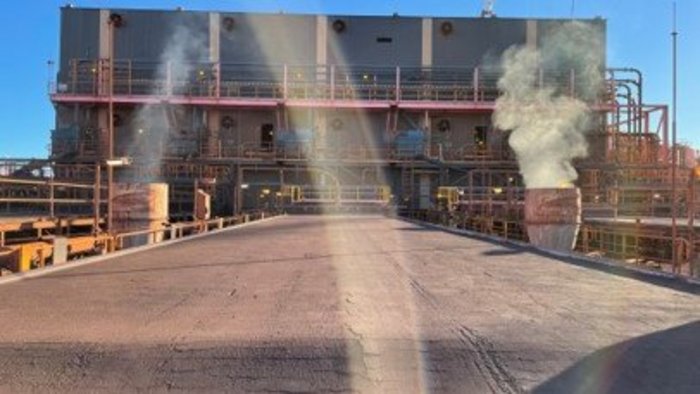
For more information please also have a look at our news:
DELKOR MAX-FEED: REDUCING COSTS WHILE INCREASING PERFORMANCE OF VACUUM BELT FILTERS
References
-
Horizontal Belt Filters in India
Customer Project Name Uranium Corporation of India (UCIL) India 2010 Fabrication, supply and installation of horizontal belt filters
The horizontal belt filters were supplied for UCIL's Tumalapalle Uranium Processing Plant, consisting of eleven 110 m² and one 5 m² filters. The twelve belt filters filter leached slurry from the alkali pressure leach autoclave (110 m² filters) and one to filter yellow cake (5 m² filter).
-
Horizontal Belt Filters in Australia
Customer Project Name Hope Downs Mine Australia 2013 Belt filter assemblies with vacuum filtrate systems
DELKOR supplied two 85 m² horizontal belt filters for Rio Tinto Iron Ore’s Hope Downs 4 Iron Ore Fines Processing Plant. The filters were manufactured in China, South Korea and Australia and were assembled in Perth, Australia before being trucked to site 1,200 km away.
Project figures
2 x 85 m² HBF‘s 461 dtph design
-
Value for Money
- Efficient and reliable liquid/solid separation equipment
-
Efficiency
- We design, fabricate and supply a wide-range of horizontal vacuum belt filters that are suitable for dewatering a wide-range of material types, including the de-watering of process plant tailings
-
Service
- Since our gravity sand filters use sand as the filtering media, we do away with valves, pilot mechanisms, rate controllers, guagues and air compressors
-
Reference
- We remain the supplier of the world's largest individual machine and filtration plants around the world
CONTACT US
Do you have any questions or would you like further information?
We look forward to your inquiry at: info@takraf.com